Welcome to our Blog!
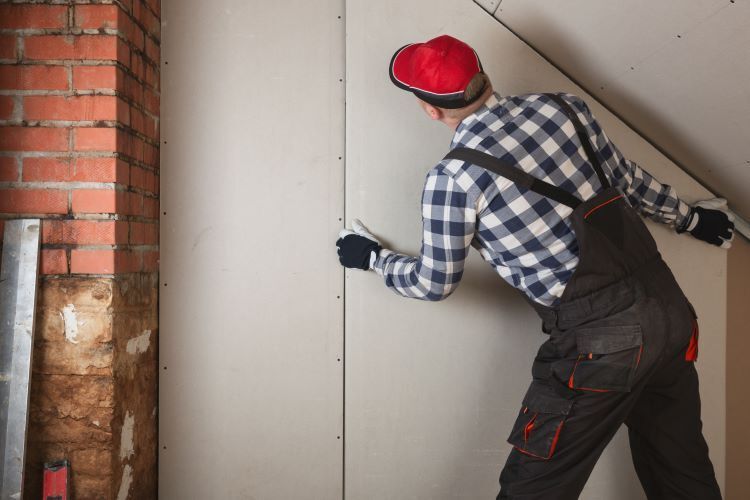
Installing drywall is a key step in transforming any space, whether it’s a new construction project or a home renovation. However, the success of drywall installation largely depends on how well the walls are prepared beforehand. At Barrie Drywallers , we know that proper preparation is the foundation of a smooth and efficient installation process. Here's a step-by-step guide to getting your walls ready for drywall installation . 1. Clear the Area Before you begin, ensure that the workspace is clean and clutter-free. Move furniture, cover floors with drop cloths, and remove any obstacles that might hinder the installation process. Why This Matters: A clean and open workspace minimizes the risk of damage and allows installers to work efficiently. 2. Inspect the Walls Carefully examine the walls for any issues that could affect the drywall installation, such as cracks, water damage, or uneven surfaces. What to Look For: Cracks or Holes: Repair these to provide a stable surface. Moisture or Mold: Address these issues immediately to prevent future damage. 3. Address Insulation Needs If your walls lack proper insulation, now is the time to install or upgrade it. Adequate insulation not only improves energy efficiency but also enhances soundproofing. Pro Tip: In areas prone to moisture, like basements, consider using moisture-resistant insulation materials. 4. Ensure Proper Framing Check that the wall studs are properly spaced and securely installed. The standard spacing for studs is 16 or 24 inches apart. Ensure they are level and aligned to avoid uneven drywall. Tools You’ll Need: Level: To check for straightness. Measuring Tape: To confirm correct spacing. 5. Install Vapor Barriers In areas like basements or bathrooms, adding a vapor barrier is crucial to prevent moisture from seeping into the walls. Material Options: Plastic Sheets: Cost-effective and easy to install. Specialized Paints: Ideal for areas requiring a seamless application. 6. Pre-Plan Electrical and Plumbing If your project involves electrical wiring or plumbing, make sure all these elements are installed and secured before drywall installation. Mark their locations clearly on the studs to avoid accidentally covering access points. What to Check: Ensure electrical boxes are flush with the intended drywall surface. Verify that plumbing pipes are securely anchored. 7. Clean and Prime the Surface Dust and debris on the walls can interfere with drywall adhesion. Use a broom, vacuum, or cloth to thoroughly clean the wall surface. Optional Step: Apply a primer to improve the adherence of joint compounds and paint after the drywall is installed. 8. Gather the Right Tools Having the necessary tools and materials on hand ensures a smooth installation process. Checklist: Drywall sheets Screws or nails Drywall tape and joint compound Utility knife and drywall saw Screw gun or drill Why Choose Barrie Drywallers? At Barrie Drywallers , we understand that a flawless drywall installation begins with meticulous preparation. Here’s why our clients in Barrie, Ontario, trust us: Expertise: Our experienced team knows the ins and outs of drywall preparation and installation. Quality Materials: We use only top-tier materials for durable, long-lasting results. Attention to Detail: We ensure every step is done right, from framing to finishing. Local Knowledge: As a trusted local company, we understand the unique needs of Barrie homes and businesses. Conclusion Proper wall preparation is the secret to a seamless drywall installation. By following these steps, you’ll create a sturdy foundation for your new walls, ensuring they look great and perform well for years to come. If you’re planning a drywall project and need expert assistance, Barrie Drywallers is here to help. Contact us today for professional, reliable drywall services tailored to your needs!
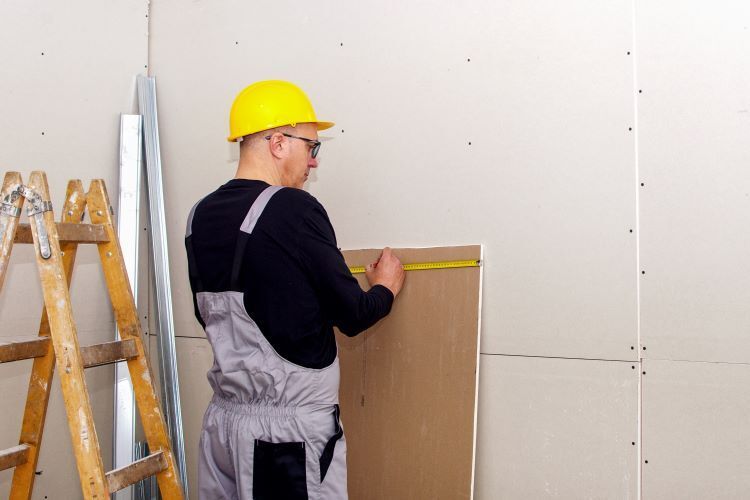
When it comes to drywall, the materials you choose can significantly impact your home's durability, appearance, and functionality. For homeowners and contractors in Barrie, Ontario, who prioritize quality and longevity, solid gypsum sheets stand out as a superior choice. At Barrie Drywallers , we believe in using only the best materials to provide flawless results that last for years. What Are Solid Gypsum Sheets? Solid gypsum sheets are drywall panels made primarily of gypsum, a natural mineral prized for its strength, fire resistance, and versatility. These sheets are sandwiched between layers of durable paper or fiberglass, resulting in a sturdy and reliable construction material suitable for various applications. Key Benefits of Solid Gypsum Sheets 1. Exceptional Durability Gypsum is naturally resilient, making solid gypsum sheets resistant to cracking and wear. This durability ensures that your walls and ceilings can withstand daily stresses, whether in a high-traffic residential area or a busy commercial space. 2. Superior Fire Resistance Safety is paramount, and solid gypsum sheets excel in fire resistance. Gypsum contains water in its mineral structure, which is released as steam when exposed to heat, slowing the spread of flames. Many solid gypsum sheets are fire-rated, making them an ideal choice for homes and businesses prioritizing safety. 3. Enhanced Soundproofing For those looking to create quiet, peaceful spaces, gypsum sheets are an excellent option. Their dense composition helps reduce noise transmission between rooms, making them perfect for offices, bedrooms, or entertainment areas. 4. Moisture and Mold Resistance In a climate like Barrie’s, where humidity levels can vary, moisture-resistant gypsum sheets are invaluable. These sheets are treated to resist water absorption, reducing the risk of mold and mildew growth in areas like bathrooms, basements, and kitchens. 5. Smooth and Versatile Finishing Solid gypsum sheets provide a smooth, even surface, perfect for painting, texturing, or wallpapering. Their versatility ensures a professional finish for any design style. Applications of Solid Gypsum Sheets Solid gypsum sheets are versatile and can be used in: Residential projects: Ideal for walls and ceilings in living rooms, bedrooms, and kitchens. Commercial spaces: Perfect for offices, retail stores, and restaurants needing durability and fire safety. Specialty areas: Moisture-resistant sheets are excellent for bathrooms and basements, while soundproofing options enhance theaters and recording studios. Why Choose Solid Gypsum Sheets Over Other Drywall Options? While there are various drywall options available, solid gypsum sheets stand out due to their: Longevity: Fewer repairs and replacements over time. Safety: Increased fire and mold resistance. Eco-Friendliness: Many gypsum sheets are recyclable and made with sustainable materials. Cost-Effectiveness: While slightly more expensive initially, their durability saves money in the long run. Tips for Installing Solid Gypsum Sheets Proper installation is crucial to maximizing the benefits of solid gypsum sheets. Here’s how Barrie Drywallers ensures a flawless finish: Accurate Measurements: Precise cutting minimizes gaps and ensures a seamless fit. Secure Fastening: Using the right screws and techniques to prevent sagging or movement. Expert Taping and Mudding: Achieving a smooth surface free of visible seams or imperfections. Finishing Touches: Applying primer and paint for a polished and professional look. Why Barrie Drywallers Is Your Go-To Choice At Barrie Drywallers, we specialize in using top-tier materials like solid gypsum sheets to deliver exceptional results. Our experienced team ensures that every project, whether residential or commercial , meets the highest standards of quality and durability. Conclusion Solid gypsum sheets are the ultimate choice for superior drywall, offering durability, safety, and versatility. Whether you’re renovating a home or building a new commercial space in Barrie, Ontario, investing in high-quality drywall materials will pay off in the long run. Ready to upgrade your walls with solid gypsum sheets? Contact Barrie Drywallers today for expert advice, professional installation, and unparalleled craftsmanship.
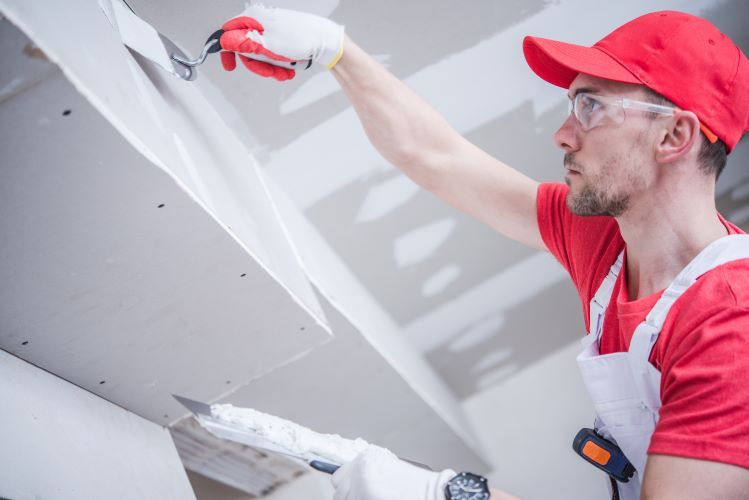
Drywall finishing is an essential step in any renovation or construction project. Whether you’re remodeling a single room or building a new home, achieving a smooth and polished look with drywall finishing can make all the difference in the final appearance of your space. At Barrie Drywallers , we understand that a high-quality drywall finish not only enhances the aesthetics of your property but also adds value and durability. In this article, we’ll walk you through the process of drywall finishing , breaking down each step to help you achieve professional results. What is Drywall Finishing? Drywall finishing involves applying joint compound (often called "mud") to the seams, joints, and screw holes of drywall sheets to create a smooth, seamless surface. The goal is to make the walls or ceilings ready for painting, texturing, or wallpapering. This process includes several stages, from applying the initial coat of compound to sanding and priming for a flawless finish. Why is Drywall Finishing Important? Aesthetic Appeal : A well-finished wall enhances the overall look of your home or office. Durability : Proper finishing helps protect the drywall from damage and wear over time. Value Addition : High-quality drywall finishing can increase the resale value of your property. The 5 Levels of Drywall Finishing Before diving into the step-by-step process, it’s helpful to understand the different levels of drywall finishing. The levels range from 0 to 5 , each representing a different degree of smoothness and readiness for paint: Level 0 : No finishing. Drywall is simply hung without any mud or tape. Level 1 : A single coat of joint compound over the tape. Often used in hidden areas like attics. Level 2 : Two coats of compound. Suitable for garages and utility spaces. Level 3 : Three coats of compound. Used for surfaces that will receive a heavy texture. Level 4 : Three coats, plus a light sanding. Ideal for walls that will be painted with a flat or satin finish. Level 5 : The highest level, with a skim coat applied for a perfectly smooth surface, ready for high-gloss paint or critical lighting. For most residential spaces, Level 4 is standard, but Level 5 is recommended for high-end finishes and areas with strong natural or artificial light. Step-by-Step Guide to Drywall Finishing Step 1: Preparation and Inspection Before you start, inspect the drywall installation to ensure all screws are properly set and the panels are securely attached. Remove any dust, debris, or protruding screws that could interfere with the finishing process. Tools Needed : Screwdriver, utility knife, sanding block. Tip : Use a shop vac to clean up dust from drywall surfaces for better compound adhesion. Step 2: Applying Drywall Tape Start by applying a layer of joint compound along the seams between drywall panels. Then, press paper or mesh tape into the wet compound to reinforce the joints. Paper Tape : Provides a stronger hold and prevents cracks. Mesh Tape : Easier to work with, especially for beginners, but may require more compound. Smooth out the tape using a 6-inch drywall knife , removing any excess compound to create a flat surface. Step 3: First Coat of Joint Compound (Mudding) Once the tape is in place, apply the first coat of joint compound over all seams, corners, and screw holes. Use a 10- to 12-inch drywall knife to feather the edges, ensuring a smooth transition between the compound and the drywall surface. Tip : Apply the compound in thin layers to avoid cracking and reduce drying time. Drying Time : Allow 24 hours for the compound to dry completely before moving to the next step. Step 4: Second Coat of Joint Compound After the first coat is completely dry, lightly sand the surface with a sanding sponge or fine-grit sandpaper to remove any ridges or bumps. Wipe away dust with a damp cloth. Apply a second coat of compound, extending it a few inches beyond the edges of the first coat to create a wider, more seamless blend. Use a larger drywall knife for this step to achieve a smoother finish. Step 5: Third Coat of Joint Compound The third coat, also known as the final coat , is applied to perfect the surface. This coat should be even thinner than the previous ones, focusing on filling in any remaining imperfections. Tip : Feather the edges as much as possible to avoid visible lines after painting. Drying Time : Again, let it dry for 24 hours before sanding. Step 6: Sanding the Surface Once the final coat is dry, it’s time to sand the entire surface to achieve a smooth finish. Use a sanding pole or a sanding block with fine-grit sandpaper for best results. Tip : Use a light source to check for imperfections. Hold a work light at an angle against the wall to highlight any uneven areas. Safety : Wear a dust mask and safety goggles to protect yourself from drywall dust. Step 7: Applying a Primer The last step in drywall finishing is applying a drywall primer to seal the surface and prepare it for paint. Priming helps paint adhere better and provides a uniform appearance. Tools Needed : Roller, paintbrush, primer. Tip : Use a high-quality primer to prevent flashing (uneven sheen) in the final paint job. Common Drywall Finishing Mistakes to Avoid Skipping the Primer : Not priming the walls can result in uneven paint coverage. Rushing the Drying Time : Applying additional coats before the previous one is fully dry can lead to cracks and bubbles. Using the Wrong Tape : Paper tape is best for flat seams, while mesh tape is better for patching small holes. Why Choose Barrie Drywallers for Your Drywall Finishing Needs? At Barrie Drywallers , we take pride in delivering high-quality drywall finishing services for both residential and commercial projects. Here’s why homeowners and businesses in Barrie, Ontario, trust us: Experienced Professionals : Our skilled team has years of experience in drywall finishing, ensuring a flawless result every time. Quality Materials : We use only the best compounds, tapes, and primers for a durable finish. Customer Satisfaction : We’re committed to providing exceptional service and exceeding customer expectations. Final Thoughts Drywall finishing is a critical step that can make or break the look of your interiors. By following the right process and using the correct tools, you can achieve a smooth, professional finish that enhances the beauty and value of your property. Whether you're tackling a DIY project or looking for expert help, Barrie Drywallers is here to assist you with all your drywall needs. Ready to transform your space? Contact Barrie Drywallers today for a free consultation and estimate on your next drywall finishing project!

Whether you're dealing with minor drywall damage or a larger hole, repairing drywall can be a rewarding DIY project if you have the right tools and materials. At Barrie Drywallers , we've helped countless homeowners restore their walls and ceilings to pristine condition, and we know that having the right supplies is key to a smooth and seamless repair. If you're planning to take on a drywall repair project, here’s a comprehensive checklist of the essential supplies you’ll need to get the job done right. With these tools, you’ll be able to handle any drywall issue, from small cracks to larger holes, and ensure a flawless finish. 1. Drywall Patch or New Sheet of Drywall For small holes or cracks, you’ll need a drywall patch. For larger holes or more extensive damage, you may need to cut out a section of the wall and replace it with a new piece of drywall. Be sure to measure the area carefully to ensure you have the correct size patch or drywall. Pre-made patches: These are great for quick repairs of small holes (typically 4-6 inches). They are easy to install and require minimal finishing work. Full drywall sheets: For larger damage, you'll need a full sheet of drywall to cut to size and install. 2. Drywall Joint Compound (Mud) Joint compound, often referred to as "drywall mud," is the main material used to fill the gaps and seams in drywall repair. It’s essential for smoothing out joints and covering screw holes. Ready-mixed joint compound: This is the most common type and is ideal for both small and large drywall repairs. Setting-type joint compound: This type dries faster and is often used in professional drywall work. It’s great for high-humidity areas or quick fixes. 3. Drywall Tape To ensure a seamless finish, drywall tape is applied over the joints where two pieces of drywall meet. It helps to reinforce the joint compound and prevent cracking. Paper tape: Ideal for most drywall repairs, paper tape provides strong reinforcement and is widely used in professional drywall finishing. Fiberglass mesh tape: This self-adhesive tape is often used for quicker jobs or repairs on smaller holes. It is easy to apply and works well for basic repairs. 4. Putty Knife A putty knife is used to apply the joint compound (mud) to the drywall. It’s essential for smoothing the compound and creating a flush finish with the surrounding wall. 3-inch or 4-inch putty knife: Ideal for filling small holes or cracks. 6-inch putty knife: Great for larger repairs and spreading mud more evenly over wider areas. 12-inch taping knife: Used for larger areas, taping knives help smooth out the compound for a flawless finish. 5. Sanding Sponge or Sandpaper Once your joint compound has dried, you'll need to sand the area to ensure it’s smooth and level with the rest of the wall. Sanding helps remove any excess mud and leaves a seamless, professional-looking finish. Sanding sponge: These are flexible and can easily reach into corners and crevices. Fine-grit sandpaper (220-grit): This is perfect for sanding drywall and ensuring a smooth surface after applying joint compound. Pole sander: For high ceilings or walls, a pole sander can help you reach difficult areas without needing a ladder. 6. Drywall Screws or Nails If you are replacing a section of drywall, you will need drywall screws or nails to attach the new piece to the studs in the wall. Drywall screws are the most common option as they hold the drywall firmly in place. Drywall screws: These screws are specifically designed for drywall installation and have a bugle-shaped head that sits flush with the wall. Drywall nails: Though less commonly used, nails can be an option for certain projects. 7. Utility Knife A utility knife is essential for cutting drywall. Whether you need to cut a patch to size or trim edges for a smooth finish, a sharp utility knife is a must-have tool. Heavy-duty utility knife: Look for a knife with replaceable blades to ensure you always have a sharp edge for cutting through drywall. 8. Measuring Tape and Square Accurate measurements are key when cutting drywall to fit around openings or replacing sections. A measuring tape and drywall square will help you cut your drywall to the correct dimensions. Measuring tape: Ensure you measure carefully to avoid mistakes. Drywall square: A drywall square helps to make precise cuts, especially for straight edges. 9. Primer and Paint Once your drywall repair is complete and the mud is dry and sanded, it’s time to prime and paint. The primer will help seal the repaired area, and the paint will give it a smooth, finished look that blends with the rest of your wall. Primer: Use a drywall primer to ensure that your paint adheres properly to the new joint compound. Wall paint: Choose a paint that matches the existing color on your walls. You may need to apply multiple coats for full coverage. 10. Drop Cloth or Plastic Sheeting Drywall repairs can be messy, especially when sanding and applying joint compound. Protect your floors and furniture with a drop cloth or plastic sheeting. Drop cloth: Covers large areas of the floor to catch dust and debris. Plastic sheeting: Helps protect furniture or anything else in the room from dust or splashes. 11. Gloves and Safety Glasses Safety should always come first when handling drywall and tools. Protect your hands and eyes during the repair process with gloves and safety glasses. Work gloves: Protect your hands from cuts and abrasions while working with drywall and tools. Safety glasses: Protect your eyes from drywall dust and debris, especially when sanding. 12. Clean Cloth or Sponge After sanding, use a clean cloth or sponge to wipe away dust and debris before priming and painting. This ensures a smooth finish and helps your primer and paint adhere better. Conclusion With the right supplies, drywall repair can be a straightforward DIY task. Whether you’re fixing a small hole or tackling a larger project, having all the necessary tools on hand will make the job easier and help you achieve a seamless, professional-looking result. At Barrie Drywallers , we specialize in high-quality drywall repair for homes and businesses in Barrie, Ontario. If you’re not sure where to start or need expert help with your drywall project, our team is here to assist. With the right materials and techniques, we’ll ensure your walls are as good as new. Ready to get started? Contact Barrie Drywallers today for all your drywall repair needs!
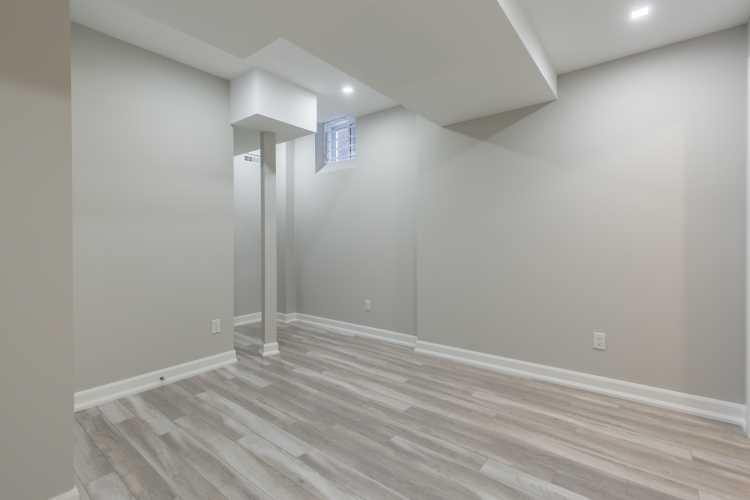
If you’re considering transforming your basement into a functional, beautiful living space, drywall installation is one of the most critical steps in the process. At Barrie Drywallers , we often get asked how long it takes to finish a basement with drywall. While the timeline can vary based on a few factors, here’s an in-depth look at what to expect from start to finish. Factors Affecting Drywall Installation Time Basement Size The size of your basement is one of the biggest factors. A smaller space can typically be completed in a shorter time, while larger basements with multiple rooms or complex layouts require more work. Complexity of Layout Basements with open floor plans are generally quicker to drywall than those with multiple rooms, unique shapes, or features like closets and staircases. Each wall and angle adds to the project’s overall complexity and time. Number of Workers The size of the crew can significantly impact the timeline. For example, a professional team with multiple workers can finish a job more quickly than a single contractor. Preparation Work Any additional prep work, like installing insulation, framing, or soundproofing, will add time to the project. It’s essential to consider these steps when planning your drywall installation. Environmental Factors The temperature and humidity levels in your basement affect the drying time for joint compound (used for taping and finishing the drywall). Cold or humid conditions can extend the timeline due to slower drying. The Typical Timeline for Drywalling a Basement Now that we know the factors influencing the project duration, let’s break down the timeline step-by-step. 1. Framing and Preparation (1-3 Days) Before installing drywall, your basement needs to be properly framed. This involves constructing a wooden or metal framework that will support the drywall sheets. For basements that are already framed, this step can be skipped, saving time. If insulation or soundproofing is required, these can also add a day or two. 2. Drywall Hanging (1-2 Days) After framing, the next step is to hang the drywall sheets. In a small to medium-sized basement, hanging drywall can take around 1-2 days. For larger basements or those with multiple rooms, this could take closer to 3 days. Professionals are efficient, using specialized tools to quickly attach drywall sheets to the framing. 3. Taping and Mudding (3-5 Days) Once the drywall is hung, taping and mudding begin. This step involves covering the seams between sheets with drywall tape and applying joint compound (mud) over the tape to create a smooth, even surface. Each coat of mud needs time to dry before sanding and adding another coat. Typically, three coats are applied, and each coat may require 24 hours to dry. Drying times can vary depending on the humidity levels in the basement. 4. Sanding and Finishing (1-2 Days) After the final coat of joint compound is applied and dried, sanding is needed to smooth out the surfaces. This ensures a seamless, clean look before painting. Depending on the basement size and the desired finish, this step can take 1-2 days. Professionals may also add a primer coat to prepare the drywall for paint. Overall Time Estimate: 7-12 Days For a standard-sized basement, the total time to complete drywall installation is around 7-12 days. Here’s a quick summary: Framing and Preparation: 1-3 days Drywall Hanging: 1-2 days Taping and Mudding: 3-5 days Sanding and Finishing: 1-2 days If additional steps like insulation or soundproofing are required, expect a slightly extended timeline. Unforeseen issues, such as extra humidity that slows drying times or necessary adjustments, may also affect the schedule. Tips for a Smooth and Timely Drywall Project To keep your basement drywall project on track, consider these tips: Prepare the Area in Advance Ensure the basement is prepped and ready for work. Clear any obstacles and handle minor repairs in advance to save time. Maintain Optimal Conditions Using dehumidifiers can help manage moisture levels, ensuring joint compound dries on time. Maintaining a stable temperature also supports quicker drying. Hire a Professional Team Professional drywallers have the skills, tools, and experience to efficiently handle your project, even if the basement layout is complex. Working with experts like Barrie Drywallers will ensure the job is done correctly and on time. Plan for Potential Delays Although professionals strive to stick to a timeline, unexpected delays can occur. Build a little flexibility into your schedule to accommodate any minor setbacks. Why Professional Drywall Installation Matters Attempting a DIY drywall project might seem appealing, but it’s a labor-intensive task that requires precision and expertise. Professional drywallers ensure each step is completed correctly, from framing and insulation to mudding and finishing, saving you time and ensuring a polished final product. With Barrie Drywallers, you can be confident that your basement’s drywall installation will be done efficiently and with attention to detail, providing a solid foundation for your finished basement. Final Thoughts Drywalling a basement isn’t an overnight project, but with proper planning, you can have a finished space ready to enjoy in about a week or two. From preparation to final touches, understanding each step can help you prepare for the time and effort involved. At Barrie Drywallers , we’re here to help bring your basement renovation vision to life with quality, timely drywall installation. If you’re ready to transform your basement or have more questions about the process, don’t hesitate to reach out to our team!
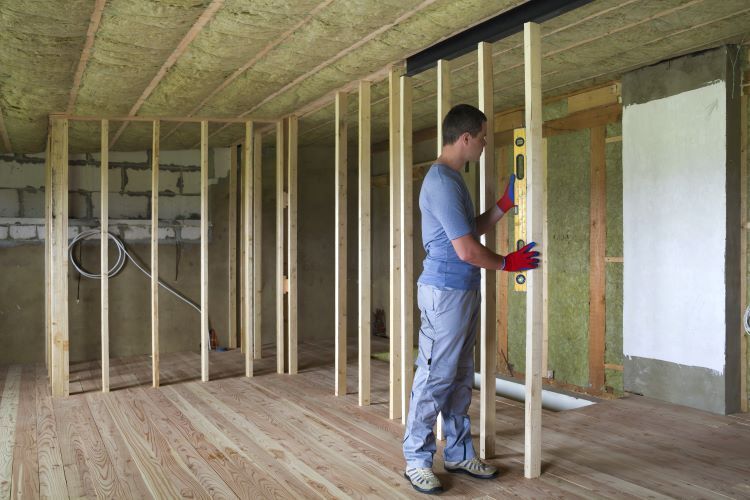
When it comes to drywall framing, choosing between metal and wood can significantly impact the durability, cost, and efficiency of your construction project. Both materials come with unique advantages and limitations, making the choice less straightforward than it may seem. For homeowners and contractors in Barrie, Ontario, understanding the specific benefits of each type of framing is essential for achieving the best results. Here, we’ll break down the differences between metal and wood drywall framing , along with considerations to help you decide which option is best for your project. Why Does Framing Matter? The framing of a wall is the structural “skeleton” that holds your drywall in place. The right framing ensures that your walls remain sturdy, soundproof, and long-lasting. It also impacts how easily electrical wiring, plumbing, and insulation can be added. With both metal and wood framing options available, your choice of material will play a key role in your project’s overall performance and aesthetics. Metal Drywall Framing Metal framing has become increasingly popular in both residential and commercial applications, and it’s especially ideal for areas with high moisture levels or the need for added fire resistance. Here are some key advantages and drawbacks of using metal framing for drywall. Advantages of Metal Framing Durability and Resistance to Moisture and Fire Metal is resistant to both moisture and fire, making it an excellent choice for basements, bathrooms, or kitchens where humidity can lead to rot and mold in wood framing. Metal framing won’t warp, shrink, or twist, ensuring a stable and durable framework over time. Pest Resistance Metal is impervious to pests, unlike wood, which can be susceptible to termites and other insects. This makes metal a long-lasting choice for structural integrity, especially in environments where pest control is a concern. Eco-Friendly and Recyclable Metal studs are recyclable, which makes them a sustainable option, especially for those concerned about the environmental impact of construction materials. Unlike wood, which involves deforestation, metal framing materials can be manufactured from recycled materials, making them an eco-friendly choice. Drawbacks of Metal Framing Higher Cost Metal framing can be more expensive than wood, which may not fit all budgets, especially in larger projects. While metal framing may provide long-term savings in maintenance, the initial investment is usually higher. Limited Insulation Metal conducts temperature, which means it can create cold spots in walls unless insulation is carefully applied. Additional measures may be necessary to ensure proper insulation, increasing labor and material costs. More Complex Installation Process Metal studs require specialized fasteners and cutting tools, and the installation process can be more complex than wood framing. Hiring a skilled contractor, like the professionals at Barrie Drywallers, ensures proper handling and installation. Wood Drywall Framing Wood remains a traditional and popular choice for drywall framing, especially in residential settings. It’s versatile, cost-effective, and widely available, but it does come with its own set of considerations. Advantages of Wood Framing Ease of Installation Wood framing is often easier to install, as wood studs are simple to cut, drill, and fasten. The material is also readily available, making it easier to source in local hardware stores. Cost-Effective Wood is typically more affordable than metal, which can make it the preferred option for budget-conscious projects. It’s a practical choice for areas of the home where high humidity and fire resistance are not primary concerns. Better for Insulation Wood naturally insulates better than metal, reducing the need for additional thermal breaks or insulation. This makes wood an efficient choice for temperature control in climates like Barrie’s, where winters can be harsh. Drawbacks of Wood Framing Vulnerability to Moisture and Fire Wood is susceptible to warping, rotting, and mold when exposed to moisture. This makes it less suitable for basements or other areas with high humidity. Wood is also combustible, which can pose a risk in areas requiring high fire resistance. Susceptibility to Pests Wood framing can be vulnerable to termites, carpenter ants, and other pests. Treating wood with pesticides and preservatives can help, but it requires ongoing maintenance. Can Shift or Warp Over Time Over time, wood can expand, shrink, or warp due to changes in temperature and humidity. This can lead to drywall cracks and structural issues if not properly maintained. Regular inspections and maintenance may be necessary to avoid these issues. Choosing the Right Framing Material for Your Project Your choice between metal and wood framing should depend on your specific needs, project budget, and the conditions of the environment where the framing will be installed. For High-Moisture Areas: Metal framing is often the best choice for basements, bathrooms, and kitchens where moisture is a concern. The moisture resistance of metal prevents rot, mold, and mildew, ensuring a stable structure in areas exposed to water. For Fire Safety Requirements: Metal is naturally fire-resistant and may be required in some commercial or high-safety applications. While wood framing can be treated with fire-resistant coatings, it doesn’t offer the same level of inherent safety as metal. For Budget-Friendly Projects: Wood framing is generally more cost-effective and easier to install, making it a great choice for most residential applications where moisture and fire resistance aren’t top priorities. For Insulation Needs: Wood framing provides better natural insulation and can help reduce heating and cooling costs. If you’re constructing in a climate with extreme temperature shifts, wood might provide more comfortable indoor conditions. Conclusion Both metal and wood drywall framing have their advantages and are suitable for different types of construction projects. Metal offers durability, moisture resistance, and fire safety, making it ideal for high-moisture or high-safety areas. On the other hand, wood is cost-effective, easy to install, and provides natural insulation, which makes it a preferred choice for most residential projects. For a professional and high-quality framing job, trust Barrie Drywallers . Our team of experts understands the unique requirements of each project and can help you make the best choice for your drywall framing needs. Contact us today to discuss your project, and let’s find the ideal framing solution to bring your vision to life.
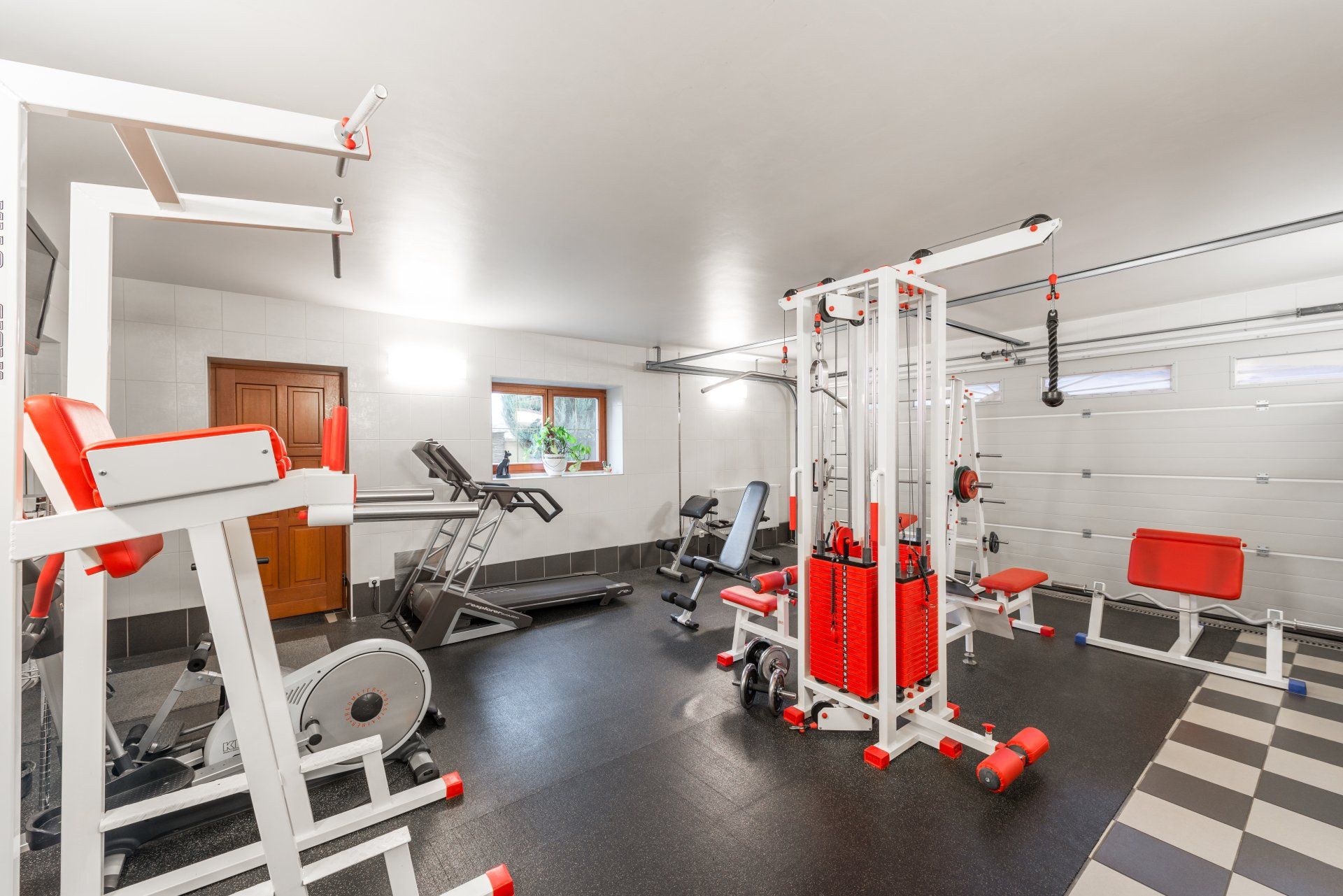
Drywall is a crucial element of most modern homes and commercial buildings. While it’s durable, drywall still requires regular maintenance to ensure it stays in perfect condition. Neglecting drywall can lead to issues like cracks, dents, water damage , and unsightly wear that could affect the aesthetics and structure of your space. At Barrie Drywallers, we specialize in all aspects of drywall care, and in this article, we'll share essential maintenance tips to keep your drywall looking pristine. 1. Inspect for Damage Regularly Routine inspection is key to identifying any small issues before they turn into major problems. Look for signs such as: Cracks around door frames and windows. Nail pops (small, raised areas where nails have pushed out of the drywall). Dents or gouges from furniture and everyday wear and tear. Water stains or damp spots, which could indicate leaks or moisture problems. Addressing these issues early on will prevent them from worsening and becoming costly repairs. For small cracks and minor damage, DIY solutions like spackling or patching may suffice. For larger areas of damage, it’s best to call professionals like Barrie Drywallers for expert repairs. 2. Keep Your Drywall Clean Dust and dirt can accumulate on your drywall over time, dulling the appearance of your walls. Cleaning your drywall occasionally will keep it looking fresh and prevent any buildup that could cause damage. Here’s how to clean drywall effectively: Use a soft microfiber cloth or dusting mop to remove surface dust. For smudges and stains, mix warm water with a gentle detergent, dip a soft sponge into the solution, and lightly clean the surface. Avoid soaking the drywall as excessive water can lead to warping or bubbling. Make sure the wall is completely dry after cleaning by using a dry cloth or allowing it to air dry. 3. Handle Small Repairs Quickly Small repairs like filling nail holes, fixing small dents, and patching minor cracks are straightforward tasks but should be done quickly to avoid further damage. Here's a simple process for handling small drywall repairs: Use spackle or joint compound to fill holes and cracks. Sand the area lightly once the filler has dried, ensuring it’s smooth and flush with the rest of the wall. Touch up the repair area with matching paint to maintain a seamless finish. If you're unsure about the process or have larger repairs, it’s wise to contact a professional to ensure quality results. 4. Prevent Moisture Buildup Moisture is one of drywall’s biggest enemies, as it can lead to mold growth and weaken the material. To prevent moisture damage: Ensure proper ventilation in rooms prone to humidity, such as bathrooms and kitchens. Fix any plumbing leaks or roof issues immediately to avoid water seeping into your walls. Install dehumidifiers in areas where moisture levels are consistently high to protect the drywall from dampness. If you notice any signs of water damage, such as discoloration, bubbling, or a musty smell, take action immediately. In cases of extensive water damage, it’s best to replace the affected drywall section and investigate the root cause of the moisture. 5. Protect Your Drywall from Impact Damage While drywall is durable, it can be prone to dents, scuffs, and scratches, especially in high-traffic areas like hallways or kids' playrooms. Here are a few tips to prevent impact damage: Use furniture pads to prevent chairs and other heavy items from scuffing the walls. Consider installing wall guards or wainscoting in areas that are prone to damage. Encourage the use of door stops to prevent doors from slamming into drywall and causing damage. By taking preventative measures, you can extend the life of your drywall and keep it looking great for years to come. 6. Repaint as Needed Over time, the paint on drywall can fade, crack, or chip, leading to an outdated or worn appearance. Regularly repainting your walls not only keeps them looking fresh but also adds an extra layer of protection. Before painting: Clean the walls to remove any dirt or debris. Repair any small cracks, holes, or imperfections. Use a primer to ensure smooth paint application and improved adhesion. Choose high-quality paints with a durable finish, especially in high-traffic areas, to minimize wear and tear. 7. Address Nail Pops and Joint Tape Issues Over time, nail pops (when nails protrude slightly from the drywall) and issues with joint tape (bubbling or peeling) can occur, especially in older homes or buildings that experience shifts. To address these: For nail pops, remove the raised nail and replace it with a drywall screw, then patch the area with joint compound. For joint tape, remove the damaged section, apply a new layer of joint compound, and add fresh tape. Once dry, sand the area smooth and repaint as needed. These repairs should be done carefully to ensure a seamless finish, so if you're unsure, consider hiring a professional like Barrie Drywallers to handle the job. 8. Consult a Professional for Large-Scale Repairs While many drywall issues can be handled with simple DIY methods, larger problems such as extensive cracking, water damage, or structural issues require professional attention. Experienced drywall contractors can assess the problem and provide the best solution, whether it’s a patch job, a partial replacement, or even a full drywall installation. At Barrie Drywallers, we have the tools and expertise to handle all kinds of drywall maintenance and repairs, ensuring your walls remain in top condition. Conclusion Maintaining your drywall is essential for preserving the appearance and integrity of your home or commercial space. By performing regular inspections, cleaning, and addressing minor repairs, you can prevent costly damage and keep your walls looking pristine. For major repairs or if you’re unsure about how to fix a problem, don’t hesitate to contact Barrie Drywallers for professional drywall maintenance services. With the right care and attention, your drywall can last for years, providing a smooth, attractive finish to your home or building.

Finishing drywall in your garage is an essential step in creating a functional and aesthetically pleasing space. Whether you use your garage for parking, storage, or as a workshop, properly finished drywall can improve insulation, prevent moisture issues, and enhance the overall look of the area. At Barrie Drywallers , we’re here to guide you through the process of finishing drywall in your garage , ensuring you achieve a professional-quality result. Step 1: Gather Your Materials Before you start, ensure you have all the necessary materials and tools: Materials: Drywall sheets (typically ½ inch thick for garages) Joint compound (mud) Drywall tape (paper or mesh) Primer and paint Tools: Utility knife T-square or straight edge Drywall saw Drill or drywall screws Mud pan and taping knife Sanding block or sponge Safety goggles and dust mask Step 2: Install the Drywall Begin by installing the drywall sheets on the walls and ceiling of your garage: Measure and Cut: Measure the height and width of the wall sections. Cut the drywall sheets to size using a utility knife and T-square. Attach the Drywall: Secure the drywall to the studs with drywall screws. Place screws every 16 inches along the edges and every 24 inches in the field. Make sure the screws are slightly recessed but not so deep that they break the paper surface. Install Ceiling Drywall: If you are drywalling the ceiling, work in the same manner. It’s often easier to have help for this part, as it can be tricky to hold the sheets overhead. Step 3: Tape the Seams Once the drywall is installed, it’s time to tape the seams to create a smooth, continuous surface: Apply Joint Compound: Using a taping knife, spread a thin layer of joint compound over the seams and screw heads. Aim for about 4 to 6 inches wide. Embed the Tape: Cut the drywall tape to size and press it into the wet joint compound. Use your taping knife to smooth it out, ensuring there are no bubbles or wrinkles. Cover the Tape: Apply another layer of joint compound over the tape, feathering the edges to blend it into the surrounding drywall. Step 4: Apply Additional Coats of Joint Compound To achieve a smooth finish, you’ll need to apply at least two more coats of joint compound: First Coat: Allow the first coat to dry completely, which typically takes about 24 hours. Sand the Surface: Once dry, lightly sand the area with a sanding block or sponge to smooth out any rough spots. Be sure to wear a dust mask to avoid inhaling drywall dust. Second Coat: Apply a second coat of joint compound, extending further beyond the first coat to create a seamless transition. Allow it to dry and sand again. Final Coat: For the final coat, use a wider taping knife to feather the edges even more. Sand once it’s dry to achieve a flawless finish. Step 5: Prime and Paint After finishing the drywall, it’s time to prime and paint to protect the surface and improve aesthetics: Prime the Surface: Apply a coat of drywall primer to seal the joint compound. This helps the paint adhere better and prevents uneven absorption. Paint: Choose a durable paint suitable for garages, such as latex paint, which can withstand moisture and stains. Apply at least two coats for even coverage. Step 6: Consider Additional Features Once your drywall is finished, consider adding features that enhance the functionality of your garage: Insulation: If your garage is not already insulated, adding insulation can improve energy efficiency. Shelving and Storage: Consider installing shelves or cabinetry for additional storage options. Lighting: Ensure you have adequate lighting for any tasks you’ll perform in the garage. Conclusion Finishing drywall in your garage can significantly enhance the space's functionality and appearance. With proper materials, careful attention to detail, and a step-by-step approach, you can achieve a professional-quality finish. At Barrie Drywallers , we specialize in drywall installation and finishing, ensuring that your project is completed to the highest standards. If you need assistance or prefer to leave it to the professionals, don’t hesitate to contact us for expert drywall services in Barrie, Ontario. Transform your garage into a well-finished space today!

Popcorn ceilings, also known as acoustic or textured ceilings, were a popular design trend from the 1950s to the 1980s. However, many homeowners today prefer smooth, modern ceilings and opt to remove the outdated popcorn texture. While removing a popcorn ceiling can dramatically transform the look of a room, there are several important factors to consider before diving into the project. At Barrie Drywallers, we specialize in popcorn ceiling removal and are here to help you understand what’s involved in the process. 1. Asbestos Testing and Safety One of the most critical things to consider before removing a popcorn ceiling is whether it contains asbestos. Popcorn ceilings installed before the 1980s often used asbestos as a fire-retardant material. Disturbing these ceilings can release dangerous asbestos fibers into the air, posing serious health risks. How to Check for Asbestos: If your home was built before the 1980s, it’s essential to have a sample of the ceiling tested by a professional asbestos testing service before beginning any removal. If the test comes back positive, do not attempt to remove the ceiling yourself. Instead, hire a licensed asbestos abatement professional to safely remove or encapsulate the material. At Barrie Drywallers, we always recommend testing for asbestos before any popcorn ceiling removal project to ensure the safety of your home and family. 2. Preparation for Mess and Dust Removing a popcorn ceiling is a messy job that creates a significant amount of dust and debris. The texture, once scraped off, leaves behind loose material that can coat surfaces throughout the room. Steps to Prepare the Room: Cover floors, walls, and furniture with plastic sheeting to protect them from falling debris. Use masking tape to seal off doorways and vents to prevent dust from spreading to other areas of your home. Consider removing furniture from the room entirely, if possible, to avoid cleaning up dust afterward. Wearing a dust mask or respirator, goggles, and protective clothing is essential to protect yourself from inhaling particles during the removal process. 3. Ceiling Condition and Repairs Once the popcorn texture is removed, you’ll have a clear view of the ceiling’s condition. In some cases, imperfections or damage may be hidden beneath the textured surface, such as cracks, water stains, or poorly finished drywall seams. Common Issues After Removal: Cracks or holes in the ceiling may need to be patched before you can proceed with smoothing the surface. The drywall may require additional sanding or even a fresh layer of joint compound to create a uniform, smooth finish. If you find water damage, you’ll need to address the source of the issue before repairing and repainting the ceiling. At Barrie Drywallers, we can assess and repair any ceiling imperfections that may be revealed during the popcorn ceiling removal process, ensuring a flawless result. 4. Choosing a New Ceiling Finish Once your popcorn ceiling is removed, you’ll need to decide how to refinish the ceiling. There are several options available depending on your style preferences and budget. Popular Ceiling Finish Options: Smooth Finish: A clean, sleek look that’s ideal for modern homes. This option requires careful sanding and application of joint compound to achieve a perfectly smooth surface. Textured Finish: If you prefer a bit of texture, you can opt for a lighter finish, such as knockdown or orange peel texture. These add subtle visual interest without the dated look of popcorn. Painted Ceiling: Whether you choose a bold color or classic white, a freshly painted ceiling can enhance the look of your room and tie your design together. Barrie Drywallers can provide expert guidance on selecting the right finish for your ceiling, as well as professional painting services to give your ceiling a polished look. 5. Time and Cost Considerations Popcorn ceiling removal is a time-consuming project, especially if you're dealing with a large area or damaged ceiling. The complexity of the job can also affect the overall cost. Factors Affecting Time and Cost: Size of the room: Larger rooms or homes with high ceilings will take longer and may require more materials. Ceiling condition: If the ceiling is in poor condition or needs extensive repairs, this will add to the time and cost. Finishing choices: A smooth ceiling finish may require more labor-intensive work compared to adding a textured finish. While some homeowners may attempt a DIY popcorn ceiling removal, it's often worth hiring professionals like Barrie Drywallers to ensure the job is done efficiently, safely, and with the best possible outcome. Conclusion Removing a popcorn ceiling can dramatically update the look of your home, giving it a more modern, fresh appearance. However, there are important things to consider before taking on this project, from asbestos testing to the final ceiling finish. Whether you're worried about the mess, concerned about hidden ceiling damage, or simply want to ensure a flawless result, Barrie Drywallers can help you every step of the way. If you're ready to say goodbye to your popcorn ceiling, contact us today for professional, safe, and high-quality removal services!
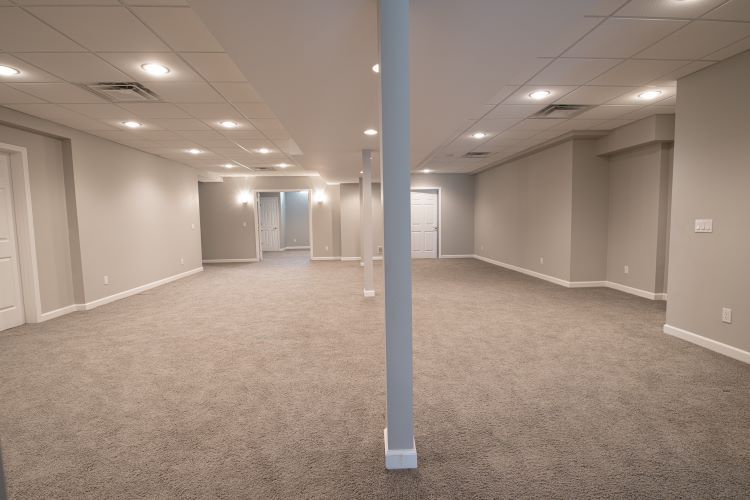
When it comes to increasing the value of your home, drywall might not be the first thing that comes to mind. However, this essential building material plays a key role in the overall look, function, and integrity of your property. Whether you are renovating your home, preparing it for sale, or simply upgrading your space, quality drywall installation can have a significant impact on your property’s worth. In this article, we’ll explore how drywall can enhance the value of your home and why professional drywall installation by Barrie Drywallers is a smart investment. 1. Smooth, Clean Walls Make a Strong First Impression First impressions matter, especially when potential buyers step into your home. Drywall creates the smooth, clean surfaces that form the foundation of your interior walls and ceilings. Well-installed drywall helps your home look modern, fresh, and well-maintained, while poorly installed or damaged drywall can make rooms feel neglected and dated. Buyers tend to focus on visible imperfections when viewing a home, so unsightly drywall issues like cracks, dents, or uneven surfaces can give them pause. Investing in high-quality drywall installation ensures that your home’s interior looks pristine, making it more appealing to buyers and increasing its market value. 2. Energy Efficiency and Insulation One of drywall’s lesser-known benefits is its role in enhancing your home’s energy efficiency. Drywall serves as an excellent barrier for insulation, helping to regulate indoor temperatures and reduce energy costs. Homes that are energy-efficient are increasingly sought after by buyers, as they can lead to long-term savings on utility bills. In Barrie, Ontario, where winters can be particularly cold, properly installed drywall paired with insulation helps keep homes warm and cozy. This energy efficiency factor can be a major selling point, as buyers are often willing to pay more for homes that offer lower heating and cooling costs. 3. Fire and Moisture Resistance Drywall is available in specialized types that offer additional benefits, such as fire resistance and moisture resistance. Fire-rated drywall, often called "Type X," is designed to slow the spread of fire, providing an extra layer of protection for your home. Installing fire-resistant drywall in areas like garages, basements, and utility rooms can increase your home’s safety and add to its overall value. Similarly, moisture-resistant drywall is ideal for bathrooms, kitchens, and basements, where high humidity levels or water exposure are common. Homes that feature moisture-resistant drywall are less prone to mold and water damage, which can be expensive to repair and detrimental to your home’s value. Using the right type of drywall in moisture-prone areas ensures your home is protected and maintains its worth over time. 4. A Foundation for Modern Design Drywall provides the perfect canvas for modern interior design. Whether you prefer a minimalist aesthetic or bold accent walls, drywall gives you the flexibility to achieve a variety of design styles. A clean, smooth surface allows for easy application of paint, wallpaper, or texture finishes, letting you customize your home to reflect your personal taste or current market trends. Homes with modern, updated designs tend to attract more buyers and command higher prices. When it comes to renovations, drywall is a crucial component in transforming outdated spaces into stylish, contemporary rooms that appeal to today’s buyers. 5. Increased Durability and Longevity High-quality drywall installation ensures that your walls and ceilings are durable and long-lasting. Drywall that is professionally installed by experts like Barrie Drywallers is less likely to suffer from cracks, holes, or other damage over time. This durability is important for maintaining the value of your home, as buyers are more likely to pay a premium for properties that require less maintenance and repair . Additionally, if you’re planning to live in your home for many years, investing in durable drywall will help you avoid costly repairs down the road, preserving your home’s worth for future resale. 6. Adds Value During Renovations Home renovations are one of the most effective ways to increase your property’s value, and drywall plays a pivotal role in the success of these projects. Whether you’re finishing a basement, adding an extension, or remodeling a bathroom, new drywall is an essential part of the renovation process. Installing fresh drywall can instantly refresh and modernize a space, making it more attractive to both current homeowners and future buyers. Drywall also provides the structural foundation needed for electrical wiring, plumbing, and insulation, making it an integral part of any home improvement project. A professional drywall installation ensures that all aspects of the renovation come together seamlessly, adding long-term value to your home. 7. Cost-Effective Home Improvement One of the reasons drywall is so widely used in construction and home improvement is its cost-effectiveness. Drywall is relatively affordable, making it an accessible option for homeowners looking to improve their property’s worth without breaking the bank. The return on investment (ROI) for drywall installation is often high, especially when paired with other upgrades like new flooring, lighting, or paint. By choosing Barrie Drywallers for your drywall installation or repair, you’re making a cost-effective decision that can yield significant value for your home in the long run. Conclusion When it comes to increasing the value of your home, drywall is an often-overlooked factor that can make a big difference. From creating smooth, attractive surfaces to improving energy efficiency and durability, drywall plays a key role in enhancing your home’s overall worth. Whether you’re planning a renovation or simply want to ensure your home looks its best, investing in professional drywall installation is a smart move. At Barrie Drywallers , we specialize in high-quality drywall services that are tailored to meet your specific needs. Our team of experienced professionals is dedicated to delivering flawless results that can boost your home’s value and aesthetic appeal. Contact us today to learn how we can help with your next drywall project and improve your property’s worth.